LONG WAITS
AND HIGH PRICES
The impact of today’s supply chain woes on construction projects
September 22, 2021
The construction industry is experiencing volatile market conditions. Shortages are popping up across the supply chain, and material costs are rising. Not surprisingly, these conditions are impacting project costs and timelines. With cost increases and delays changing daily, how can design professionals and general contractors help you navigate your new construction project? We examine some of the root causes of these conditions, the effect on construction projects, what to know before you start your project, and how designers and general contractors can minimize impacts to your project budget and schedule.
What’s Causing Supply Chain Issues and Price Increases?
A convergence of factors – scaled-down production, high demand for construction materials, and labor shortages – is the source of supply chain issues and price increases.
When the pandemic began, demand for construction materials fell. Manufacturers slowed production in response. When demand for materials like lumber, steel, plastic, and aluminum increased again, there wasn’t enough supply.
The winter storm that battered Texas in February and the Suez Canal blockage in March further disrupted the construction supply chain. According to the Associated General Contractors of America (AGC), the winter storm shut down industrial plants that supply raw materials for construction plastics. These plastics are used to make a variety of construction products. Freezing temperatures also caused PVC pipes to burst, which increased demand for materials already facing delays. More recently, Hurricane Ida shut down several ports in the Louisiana area, which experts say will cause more supply chain problems.
The industry also lacks drivers to transport materials from mills to dealers.
In short, there is high demand for construction right now and not enough supplies. Speeding up production isn’t a simple solution either – construction materials take time to produce and transport. So, suppliers will struggle to meet the high demand for construction projects in the commercial and residential market sectors.
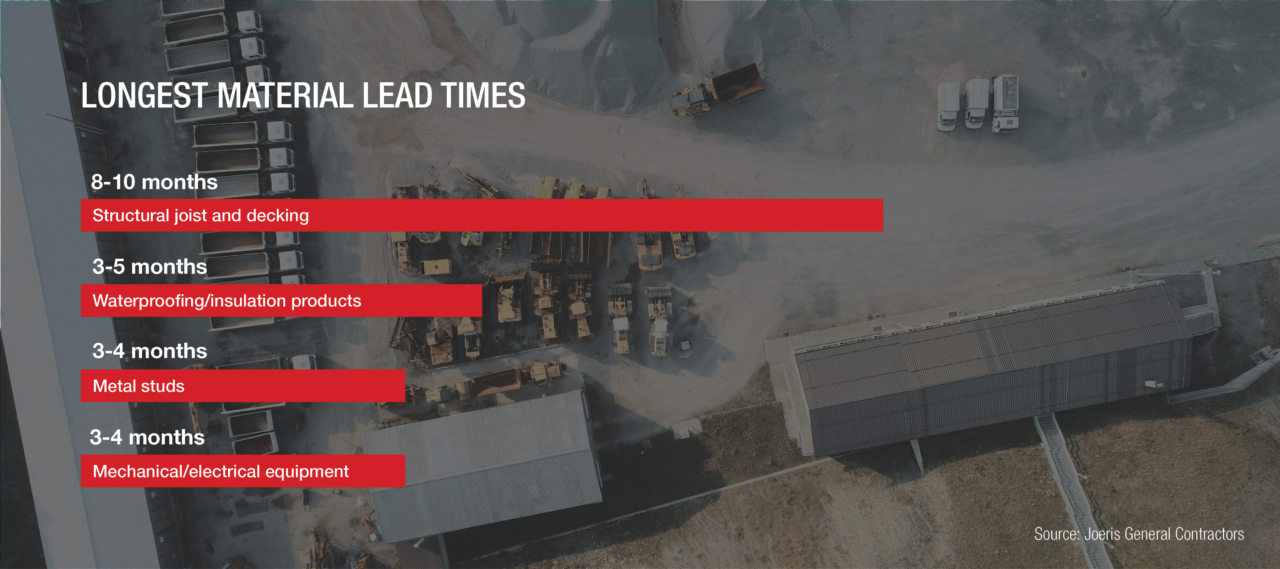
The Impact on Construction Projects
Construction projects now face longer completion times and higher costs due to supply chain issues and inflation. According to the AGC, there are delays at every level of the supply chain.
Structural joist and decking, waterproofing and insulation products, metal studs, and mechanical and electrical equipment have the longest delays, according to Russell Syma, Director of Pre-Construction for Joeris, a general contracting firm headquartered in San Antonio. He says structural joist and decking – both essential components in steel building construction – have the longest lead times, at 8-10 months.
The cost of materials has also skyrocketed, with some increasing by 100% since last summer. “Typically, yearly inflation rates for total construction cost hold between 2% to 4%; however, 2021 is proving to be an increase of 7% to 9%,” says Syma.
If you put a construction project on hold during 2020, the cost estimates and projected construction timelines may not be accurate. Your project may also require additional design fees as architects perform value engineering, assess material substitutions, or redesign project elements to fit within the budget.
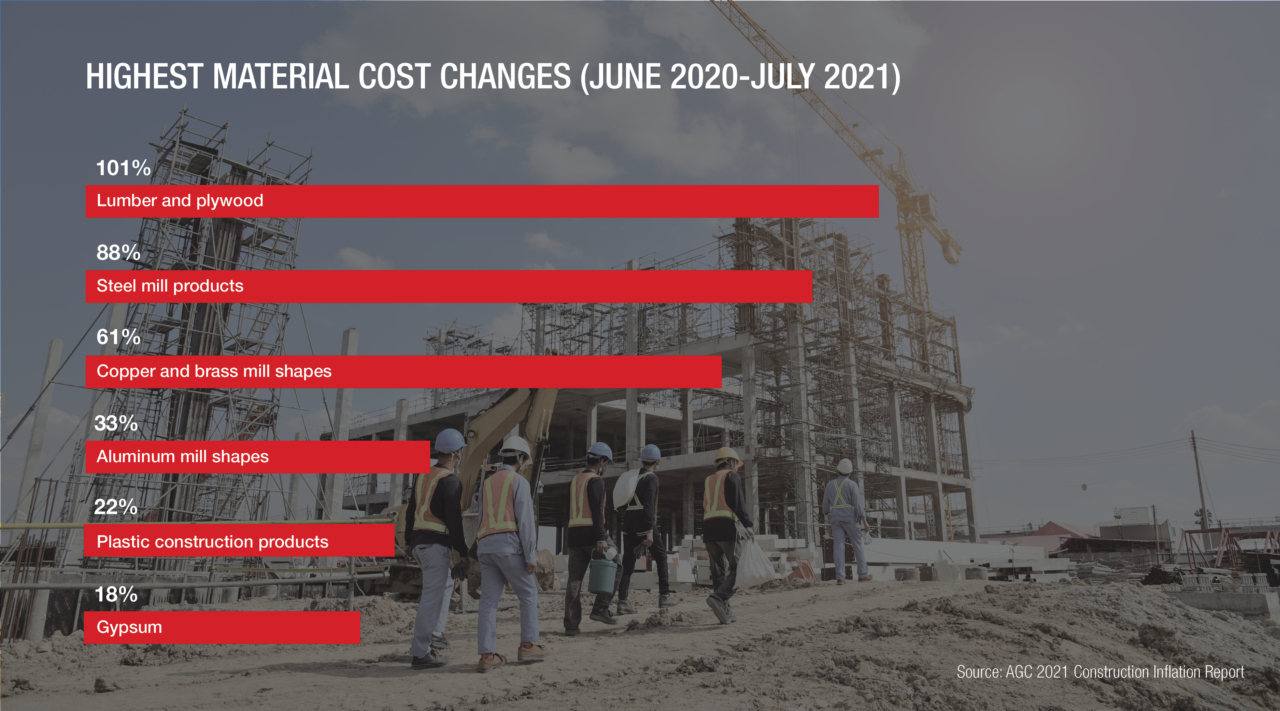
What to Know Before Starting Your Projects
Whether you’re starting a new project or resuming one you put on hold, here are three things to prepare for as you begin the process.
Be prepared to evaluate the pros and cons of choosing alternate materials
Material approval and orders are key to keep projects on track. If your material is delayed, your design professional and general contractor can help you weigh the pros and cons of choosing an alternate material. But you may have to make tough decisions about substitutions. An alternate material may arrive faster but carry a higher price tag. Also, some materials may not delay your project as much as the lead time suggests. For example, a material may have a four-month lead time but isn’t needed until two or three months into construction; as a result, it may only delay your project by a month or two.
Inflation and supply chain issues are hard to predict, and they may not end soon
Price increases and delays can fluctuate from week to week. “Metal studs have experienced month-over-month cost increases over the past year,” says Syma. “PVC pipe pricing is currently uncertain due to plant shutdowns related to Hurricane Ida.”
They might last for the foreseeable future, too. “There currently does not appear to be an end in sight for escalation and delays surrounding steel products,” says Syma. “These escalations will likely be exacerbated by the rise in the number of construction projects, especially in Texas. School bonds are coming back, private development is returning, and the new infrastructure bill will bring additional projects to our state.”
There isn’t a one-size-fits-all solution for every project
When it comes to the best solution for your project, there’s no rule of thumb. We must evaluate each project on a case-by-case basis for cost and schedule savings. What makes sense for another project may not be the best option for your project.
Strategies to Minimize Delays and Budget Increases on Your Project
Designers and general contractors can’t control price increases and material delays, but we can take the following measures to help your project run as smoothly as possible.
Get the contractor involved early
Contractors can identify which materials to order early, which can minimize delays down the road. They can also provide ways to cut costs, especially on materials. “Most often this comes down to identifying the appropriate building systems, based on cost and availability, and ensuring the project is appropriately phased to allow materials to be procured in alignment with the current market conditions,” says Syma.
Know which materials have longer lead times
Architects and interior designers can also talk with manufacturer representatives before specifying materials for your project to prevent delays and change orders later in the construction process.
Practice good communication
Communication creates trust between the owner, contractor, and designer. Trust matters when ordering materials early and making tough decisions about material substitutions, cost, and schedule. “Mitigating delays and price increases all come down to having a plan and ensuring the owner and contractor have effectively provided a path for releasing trade partners as early as possible,” says Syma.
Owners, architects, and general contractors must work closer together than ever before to adjust to current market conditions. While your project will likely experience price increases and delays, knowing what to expect and having a project team who knows how to navigate these issues will keep your stress levels low and help your project run more smoothly.
About the Author
Carlos Gonzalez RID, LEED AP
As a registered interior designer, Carlos has a passion for design and improving the built environment. He helps clients navigate the construction process to create spaces that reflect an organization’s values, goals, and culture.